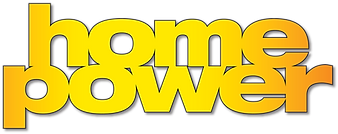
Home Power magazine was published from October 1987 to November 2018. Throughout its 31-year history, Home Power played a central and indispensable role in the mainstreaming of residential-scale renewable energy systems. It provided a first-of-its-kind networking hub for end-users, professional installers, and equipment manufacturers to interact, share ideas, and advance the use of renewable energy, energy efficiency, and electric vehicles.
Home Power's visionary founders, Karen, and Richard Perez were part of the cultural awakening that was San Francisco in 1968. In 1970 they headed north to homestead a piece of off-grid property in a remote corner of southwestern Oregon called Agate Flat. In 1982, Karen and Richard purchased their first solar-electric module, and it sparked the vision that would grow into Home Power.
With the help of family and friends and the first Macintosh computer, Karen and Richard founded Home Power, “The Hands-On Journal of Home-Made Power,” in 1987. The publication quickly became a platform for end-users and professionals alike to share their experiences designing, building and living with renewable power systems.
This site hosts Home Power’s complete 31-year archive. The content encapsulates three decades of the history of the renewable energy movement in the U.S. and beyond. Each issue is available for non-commercial use at no cost to registered members of this site. To download issues, create a free account.
Actions that originate from people, organizations, and movements occur at a given place and time. The act itself may be a quick flash of an idea or a sustained effort like Home Power that crosses decades. We hope that Home Power's archive content will continue to educate and inspire clean energy advocates everywhere, for years to come.